خوردگی بتن چیست ؟
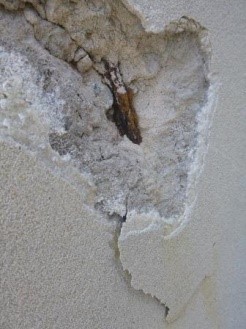
اصطلاح خوردگی ، جهت بروز فعل و انفعالاتی که تخریب زودرس بتن را به همراه دارد ، گرفته شده است. ازدیاد حجم فولاد درون سازه بتنی بر اثر واکنش های شیمیایی / الکتروشیمیایی ، سبب افزایش فشار درون بتن گردیده که در نهایت فرایند تخریب بتن را به همراه دارد. در این مقطع ترمیم بتن مطلقا امکان پذیر نبوده و یا انجام آن با هزینه های گزافی همراه است. شباهت این فرایند در بتن با بیماری مهلک سرطان عنوان سرطان بتن (Concrete Cancer) را مطرح نموده است. اما فرایند تخریب بتن های غیر مسلح به گونه دیگری است و واکنش های قلیایی سنگدانه ها می تواند یکی از علت های آن باشد .
کاویتاسیون بتن چیست ؟
کاویتاسیون یا حفره نوع دیگری از خوردگی بتن است که یک فرایند فیزیکی است که به دلیل افزایش فشار محلی در اثر سقوط حباب های بخار ، باعث سوراخ شدن سطح می شود. حفره به روش های زیر می تواند به بتن آسیب برساند:
1. به دلیل امواج شوک تولید شده توسط انفجار حباب
2. توسط میکرو جت ها به دلیل انفجار حباب
3. فروپاشی خوشه های حباب دار
کاویتاسیون به طور کلی در کانال هیدرولیک و لوله ای اتفاق می افتد که سرعت جریان به طور تیپیکال بیش از 10 متر در ثانیه در دما و فشار طبیعی است. مایع با سرعت بالا منطقه ای از فشار زیر جوی را ایجاد می کند که منجر به تشکیل حباب های بخار می شود. این حباب های بخار در نهایت فرو می ریزد (انفجار) و باعث ضربه به سطح بتن می شود.
فشار ممکن است به دلیل انفجار این حباب ها به چند صد مگا پاسکال برسد. اثر مداوم ممکن است در نهایت سطح بتن را شل کند. اختلال جریان اثر کاویتاسیون را بدتر کرده و سرعت آسیب را تسریع می کند. در حالی که قسمت بزرگی از بتن آسیب دیده است ، اثر کاویتاسیون به تدریج کاهش می یابد. کاویتاسیون بر اثر تغییر ناگهانی در سرعت ، جهت آب و افت فشار منجر به حفره بر اثر پدیده خلأزایی می گردد به عبارت دیگر هر زمان که فشار در نقطه ای از مایع به دلیل بی نظمی در سطح جریان به حد فشار بخار کم شود ، حباب هایی در مایع جاری تشکیل می گردد ، این حباب ها با مایع به سمت پایین دست جریان حرکت کرده و به هنگام ورود به منطقه ای پر فضار با ضربه می ترکند ، ترک های مکرر حباب ها در نزدیکی سطح بتن سبب کنده شدن و ایجاد چاله هایی در آن خواهد شد.همچنین مقاومت سایشی بتن در برابر کاویتاسیون رابطه مستقیمی با مقاومت فشاری و نسبت معکوس با نسبت آب به سیمان دارد همچنین این مقاومت به دانه بندی و جنس سنگدانه ها بستگی دارد آب انداختگی و تشکیل دوغاب سخت سده در منجر به ایجادسطح شکننده و ضعیف در مقابل سایش دربتن می گردد که با تاخیر در عملیات پرداخت و ماله کشی بتن و ایجاد خلأ یا مکش در بتن می توان مقاومت سایشی بتن را افزایش داد. نوع دیگر خرابی سطح بتن ناشی از نمک ها و شوره زدگی بلورهای نمک در نزدیکی سطح بتن است. رشد بلورها مانند یخ زدگی منجر به تنش های انبساطی شده و پوسته های خمیر سیمان و سنگدانه های ریز از بتن جدا می شود سولفات منیزیم در مقایسه با سایر نمک ها خطرناکتر بوده و منجر به بلوری شدن نمک در سطح بتن و گاهی اوقات به داخل بتن از طریق منافذ موئینه نفوذ کرده و حجم زیادی را تخریب می کند.
مکانیزم کاویتاسیون در بتن و پیشگیری از آن
چگونه می توان خسارت ناشی از آب با سرعت بالا را کاهش داد؟ ما می دانیم که کاویتاسیون در جایی اتفاق می افتد که تلاطم باعث ایجاد حباب های بخار با فشار بسیار کم شود تا بتن از هم پاشیده شود.
بهترین روش برای بهبود مقاومت ، استفاده از بتن با مقاومت بالا است که احتمالاً در برابر آستر فرم جاذب ریخته می شود تا نسبت آبگیری کاهش یابد. حفره به سمت حذف ذرات بزرگتر تمایل دارد. از این رو جمع در نزدیکی سطح نباید بزرگتر از 3/4 اینچ باشد. بتن های پلیمری مقاومت خوبی از خود نشان داده اند و پوشش های انعطاف پذیر با کاهش سطح تنش در بتن زیرین ، مقداری محافظت می کنند. چنین پوشش هایی باید به شدت به بتن بچسبند تا موثر واقع شوند. برخی از پوشش های نئوپرن و پلی اورتان رضایت بخش بوده است. یکی از موارد مهم باید تهیه سطوح صاف و هم تراز و عاری از تغییرات ناگهانی شیب یا انحنا باشد.
نکاتی جهت پیشگیری از کاویتاسیون بتن
1. انتخاب اجزای تشکیل دهنده و ترکیب بتن باید بر اساس در نظر گرفتن کلیه فاکتورهای محیط و بتن باشد که می تواند بر مقاومت در برابر کاویتاسیون تأثیر بگذارد ، از جمله فاکتور اقلیمی و درجه خوردگی و فرسایش دهنده گی آب.
2.بتن باید از مقاومت و یکنواختی بالایی برخوردار باشد و مخلوط بتن باید تا حد امکان کارایی بالا داشته باشد رده بتن باید در 28 روز 400 باشد ، و رده های بالاتر فقط درصورتی توصیه می شود که افزایش قابل توجهی در مقدار سیمان نداشته باشد.
3.مقاومت بتن در برابر یخ زدگی بخصوص در لایه سطحی باید زیاد باشد. برای افزایش آن توصیه می شود از افزودنی سیلوکسان GKZh-94 به میزان 0.2٪ وزن سیمان استفاده شود که نتایج خوبی را نشان داده است. استفاده از مواد افزودنی دیگر پس از انجام تحقیقات مناسب نیز امکان پذیر است. برای ایجاد اطمینان بیشتر و بررسی کیفیت بتن تحت کاویتاسیون ، ایجاد معیار جدیدی از مقاومت در برابر یخ زدگی لایه های سطحی در معرض کاویتاسیون و ارائه روش مناسب برای تعیین آن ضروری است.
4.هم شن و هم ماسه حاوی سنگ های هواساز ، تمیز و دارای ترکیب دانه ای خوب دانه بندی شده باشندو می توان از سنگدانه درشت در بتن مقاوم در برابر کاویتاسیون استفاده کرد.
5.سطح بتن باید فشرده و صاف باشد.
خوردگی بتن به علت خوردگی آرماتور در بتن مسلح
خوردگی فولاد در بتن مسلح می تواند در سازه های بتنی مشکل ساز شود. خوردگی فولاد باعث تولید اکسید آهن یا زنگ زدگی هیدراته می شود که بسیار گسترده است. این انبساط تا زمانی که بتن خراب شود ، فشار داخلی ایجاد می کند. این عامل اصلی تخریب بتن است و مطالعات زیادی برای جلوگیری از خوردگی فولاد تقویت کننده انجام شده است.
معمولا خوردگی آرماتور در بتن و تهاجم سولفات ، از مهمترين عوامل آسيب ديدگی سازه های بتنی محسوب می شوند. بخصوص در نواحی خليج فارس به دليل وجود عناصر مخرب مانند کلريدها و سولفات ها ، اين نوع آسيب ديدگی ها بيشتر مشاهده می شود . همچنين شرايط اقليمی مانندگرما و رطوبت زياد باعث افزايش خرابی سازه ها می گردد ، زيرا دما سبب تشديد واکنش های شيميايی می شود و رطوبت برای انجام واکنش های تخريب ضروری است . در حالی که خوردگی فولاد تقویت کننده می تواند در بتن مشکل ساز شود ، اما با استفاده از مشخصات مناسب و شناسایی سریع محل های حساس می توان آن را کاهش داد. مخلوط های بتنی که برای قرار گرفتن در محیط های در معرض شرایط محیطی نامناسب طراحی شده اند ، فرصت خوردگی را کاهش می دهد. روش های آزمایشی نیز ، با ارائه یک تقریب سریع و منطقی از مقاومت در برابر خوردگی بتن ، می تواندکمک کننده باشد.
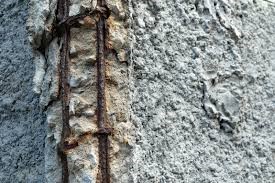
مکانیزم خوردگی فولاد
معمولا بتن شرايط مناسبی برای حفاظت آرماتور ايجاد می کند. انفعالی شدن فولاد در بتن به دلیل قليائيت زياد بتن است که حدود PH آن 13 تا 14 است . لايه محافظ يک قشر ميکروسکوپی است که بر سطح فولاد ايجاد می گردد. اين لايه محافظ فقط در PH زياد پايدار می باشد. قليائی بودن بتن به دليل وجود هيدروکسيد کلسيم است که در اثر هيدراتاسيون سيمان توليد می گردد .
دومين عاملی که از فولاد در بتن محافظت می کند ، پوشش بتن بر روی آرماتور است که يک مانع فيزيکی ايجاد می کند . اين مانع از نفوذ عناصر مخرب توليد کلريدها و دی اکسيد کربن جلوگيری بعمل می آورد . اثر پوشش بتن بعنوان يک مانع ، تابع ضخامت ، پوشش و کيفيت بتن است . خوردگی فولاد در بتن يک فرآيند الکتروشيميايی است . در اين فرآيند ، يون ها و الکترون ها بين دو قسمت مختلف سطح فولاد که در پتانسيل الکترو شيميايی اختلاف دارند ، حرکت می کنند.
اين دو بخش آند و کاتد را تشکيل می دهند ، بنابراين واکنش های الکتروشيميايی در فرآيند خوردگی را می توان به دو بخش آندی و کاتدی تقسيم نمود . در آند اکسيد شدن الکترو شيميايی صورت می پذيرد و در کاتد احياء الکتروشيميايی رخ می دهد. فلز Fe در محل آند به يون های فروز 2+ Fe تجزيه می شود و الکترون ها آزاد می گردند . برای آنکه بين بارهای الکتريکی تعادل برقرار گردد ، الکترون ها در محل کاتد مصرف شده و با ترکيب شدن با اکسيژن O2 و آب H2O تشکيل یون های هيدروکسيل OH را می دهند .ترکيب 2+ Fe و يون های هيدروکسيل تشکيل هيدروکسيد فروز 2 OH ) Fe ) می شود که يک نوع زنگ به رنگ سفيد است .
اين محصول اکسيده می شود و به صورت هيدروکسيد فريک به رنگ قرمز مايل به قهوه ای است ، همان رنگی که معمولا" در هنگام خوردگی مشاهده می شود. قدرت انبساط و تخريب محصولات خوردگی بستگی بسته به نوع محصول است . برای مثال قدرت تخريبی 3 OH ) Fe ) بيشتر از 2 OH ) Fe ) است. مهم ترين عواملی که سبب تخريب لايه محافظ ميلگرد می گردد ، کربناته شدن بتن و نفوذ يون های کلريد است. هوای معمولی دارای 3 % درصد گاز دی اکسيد کربن CO2 است . در صورت نفوذ CO2 به داخل بتن ، هيدروکسيد موجود در بتن و CO2 واکنش شيميايی انجام می دهند که منجر به تشکيل کربنات کلسيم می گردد. کربنات کلسيم باعث کاهش PH بتن می گردد و لايه انفعالی و محافظ فولاد تخريب می شود. CO2 فقط از بتن کربناته شده می تواند عبور کند ، بنابراين تمام هيدروکسيد ها بايد تبديل به کربنات شوند ، پس از آن CO2 به حرکت خود ادامه می دهد و به منطقه بتن غير کربناته می رسد . در حالی که روند کربناسيون ادامه می يابد ، تمام هيدروکسيد کلسيم ترکيب شده و در نتيجه H ـ S ـ C در حضور هيدروکسيد کلسيم آزاد می گردد تا به مصرف برسد . بنابراين در نهايت فقط سيليس هيدراته شده در بتن باقی می ماند . زيرا H ـ S ـ C در حضور هيدروکسيد کلسيم ثبات دارد و در غياب آن پايدار نبوده و تجزيه می شود .
به دليل کربناسيون بقيه محصولات هيدراتاسيون نيز تجزيه می شوند و بنابراين فقط يک شبکه سيليس ، آلومين و اکسيد آهن همراه با کربنات کلسيم تشکيل می شود . اين شبکه دارای استحکام و مقاومت زياد است و نفوذ پذيری آن نسبت به بتن اوليه کمتر می باشد . به هر حال کربناسيون از نقطه نظر خوردگی زيان آور است و سبب خوردگی آرماتور از نوع يکنواخت می گردد . يون های کلريد نيز مهمترين عوامل خوردگی آرماتور می باشند . يون های کلريد از طريق مصالح آلوده مانند سنگدانه به داخل بتن راه می يابند و يا از طريق نفوذ از محيط به داخل بتن وارد می شوند . در نقاطی از سطح فولاد که کلريد حمله می کند ، خوردگی از نوع حفره ای ايجاد می شود که اين نقاط در نقش آند می باشند و بقيه سطح فولاد به عنوان کاتد عمل می کنند . تمام کلريدها در بتن بصورت آزاد در منافذ وجود ندارند ، بلکه بخشی از يون ها با محصولات هيدروتاسيون سيمان پيوند فيزيکی و شيميايی برقرار می کنند .
مهمترين محصولی که قابليت پيوند را با يون های کلريد دار دارد، C3A است . در اثر ترکييب C3A و يون های کلريد ، محصول نمک فريدل تشکيل می گردد که از نظر خوردگی بدون خطر است . همچنين بخشی ازيون های کلريد جذب فيزيکی محصولات هيدراتاسيون می شوند که مانند نمک فريدل برای خوردگی خطر ندارند. اما کلريد های آزاد سبب تخريب لايه محافظ و خوردگی آرماتور می شوند. از آنجا که خوردگی فولاد (میلگردها) در بتن یک فرآیند الکتروشیمیایی است.در صورتی که Fe(OH)3 محصول اصلی زنگ زدگی میلگرد باشد حجم آن ۴ برابر آهن خورده نشده است و در نتیجه انبساط آن فشار زیادی به اطراف بتن وارد می کند که باعث ترک خوردگی پوشش بتنی اطراف آرماتور می شود و آرماتور بدون محافظ در معرض عوامل محیطی قرار می گیرد. ادامه خوردگی باعث کاهش تدریجی سطح میلگرد می گردد و در صورتی که تعمیرات انجام نشود تخریب و شکستگی ممکن است بطور کامل روی دهد که در این حالت عمر مفید نمونه به اتمام رسیده است. انجام فرایند خوردگی مشروط به حضور آب واکسیژن می باشد. از این رو انتظار می رود بتنی که کاملا در آب مغروق است به دلیل کمبود اکسیژن و یا بتنی که در فضای کاملا خشک (احتمالا دررطوبت زیر ۴۰ درصد) قرار دارد، خوردگی وجود نداشته باشد. عواملی در سرعت نفوذ یون کلر موثر می باشندکه شامل این موارد هستند تخلخل پوشش بتنی ، نوع سیمان و مقدار سیمان ، شرایط محیطی ، ضخامت پوشش روی آرماتور ، کربناتی شدن بتن ، وجود ترک در بتن به علت انقباض و یا مقاومت کم در مقابل یخ زدگی ، استفاده از تسریع کننده های کلروری با درصد بالا در بتن ، غلظت یون کلر در اطراف آرماتور را افزایش میدهد.
انواع خوردگی در بتن و علل آن
خوردگی به علت تهاجم سولفات ها
آسيب ديدگی بتن در معرض سولفات ها ممکن است همراه با واکنش های زير باشد :
1 – تبديل هيدروکسيد کلسيم به سولفات کلسيم که همراه با انبساط و تخريب بتن است .
2 – تبديل آلومينات ها به اترنيگايت که سبب انبساط تخريب بتن می شود .
3 – تجزيه H ـ S ـ C که سبب نرم شدن بتن و کاهش مقاومت آن می شود .
اگر سوافات کلسيم به بتن حمله کند فقط واکنش 2 رخ می دهد . اما چنانچه سولفات سديم به بتن حمله کند واکنش های 1 و 2 انجام می شود . اگر سولفات منيزيم به بتن حمله کند ، واکنش های 1 و 2 و 3 همراه با يکديگر رخ می دهد . وقتی که سولفات منيزيم به بتن حمله کند ، تمام هيدروکسيدکلسيم موجود در بتن به سولفات کلسيم تبديل می شود . به دليل فقدان هيدروکسيد کلسيم در بتن ، مقدار PH کاهش می يابد و ژل H ـ S ـ C ناپايدار می گردد . زيرا ژل هيدراته شده فقط در حضور هيدروکسيدکلسيم پايدار است و بنابراين قسمتی از آن تجزيه شده و مقدار بيشتری هيدروکسيد کلسيم توليد می گردد تا مقدار PH جبران شده و افزايش يابد . اگر سولفات منيزيم به اندازه کافی موجود باشد ، ساختارH ـ S ـ C بطور کامل تخريب می گردد و بتن نرم و اسفنجی می شود. واکنش ديگری نيز بين سولفات منيزيم و بتن انجام می شود که واکنش بين C3A و سولفات است که منجر به تشکيل اترنيگايت می شود که سبب انبساط و تخريب بتن می گردد. اترینگایت به نام میکروب بتن موسوم می باشد سولفات های محلول چون سدیم ، پتاسیم ، کلسیم و منیزیم در اغلب نقاط دنیا به طور طبیعی در آب و خاک وجود دارند. معمولاً خاک ها یا آب هایی که دارای چنین سولفات هایی هستند ، قلیایی نامیده می شوند. کلیه این سولفات ها برای بتن مضرند. سولفات ها ترکیبات مختلف سیمان هیدراته شده را مورد حمله قرار می دهند.
سولفات های سدیم و پتاسیم با هــــیدروکسید کلسیم و هــیدروآلومینات کلسیم ترکیب مــی شونـد.
محصولات واکنش های فوق عبارتند از:
1- گچ که موجب سستی سطح بتن و مقاومت آن شده ، به میزان ۱۲۵ درصد حجم مواد جامد را افزایش می دهد.
2- سولفوآلومینات کلسیم که بنام اترینگایت خوانده می شود وباعث افزایش قابل ملاحظه در حجم بتن و در نتیجه ترک و ریزش آن می گردد. میزان افزایش حجم مواد بر اثراین ترکیب به ۲۲۵ درصد می رسد.
سولفات کلسیم فقط با هیدروآلومینات کلسیم واکنش انجام می دهد که در اثر این واکنش دو شکل مختلف هیدروسولفوآلومینات کلسیم تشکیل می شود :
• منوسولفات با مقدارکم
• سولفوآلومینات کلسیم یا اترینگایت به مقدار زیاد
خوردگی به علت تهاجم کلرید ها
علاوه بر تأثیرکربناسیون ، مهمترین عامل زنگ زدگی و خوردگی آرماتور در بتن، وجود یون کلرید در آن است که ممکن است از مصالح آلوده یا مواد افزونی آغشته به کلر یا در اثر نفوذ منابع خارجی مثل محیط دریا وارد بتن گردد. یون های کلرید تنها درآب وجود دارند از این رو نفوذ کلرید مشروط به حضور آب در سیستم منفذی بتن می باشد. مکانیسم ورود یون کلرید به داخل بتن یا از طریق سیستم مکنده موئینگی است که آب آلـوده به کلـر وارد بتـن میشود، یـا ازطریق نفوذ ساده یون ها ( انتشار) در آب راکد ، وارد منافذ بتن می گردد. حالت اول مختص بتن های خشک می باشد وآب وسیله ای است که یون ها را در داخل بـتن حمل می کند. درحالت دوم ( انتشار) مختص بتن اشباع شده یا نزدیک به اشباع است ( بتن مغروق ) دربتنی که درچرخه متناوب تر وخشک قرار می گیرد هر دو مکانیسم اجرا می شود و بنابراین تحت چنین شرایطی سرعت افزا یش یافته نفوذ یون کلرید وجود دارد. معمولاً خاصیت قلیایی بالای سیمان پرتلند (PH در حدود ۱۳) منجر به ایجاد لایه محافظ نازک از اکسید فریک Fe2O3 بر روی سطح فولاد می گردد و آن را روئین و درمقابل خوردگی بیشتر محافظت می نماید. اگرچه خوردگی کلاً متوقف نمی گردد ، ولـی آهنگ آن بسیار نـاچیز بوده و درحـد قـابل قبول می باشد ، تا زمانیکه این لایه روئین کننده فولاد بر روی سطح آن باقی بماند ، بتن محیطی ایده آل برای حفاظت فولاد در مقابل خوردگی می باشد. ترکیباتی چون دی اکسیدکربن و یون کلر می توانند باعث تخریب و از بین رقتن این قشر محافظ گردند و میلگردها را در مقابل عوامل تخریبی بدون محافظ بگذارند. تمام کلریدها در بتن بصورت آزاد نیستند و بخشی از یون ها با محصولات هیدراتاسیون سیمان پیوند فیزیکی و شیمیایی برقرار می کنند. بنابراین یون های کلـــــرید در بـــتن به سه حالت پیوند فیزیکی ، شیمیایی و آزاد یافت می شوند محصول هیدرتاسیون و پیوند شیمیایی یون کلر ، تمک فریدل می باشد.
خوردگی بتن به علت کربناسیون
هوای معمولی دارای0/03 درصد گاز دی اکسید کربن co2 است که در صورت نفوذ co2 به داخل بتن ، بین هیدروکسید موجود در بتن و co2 واکنش شیمیایی انجام می گردد و کربنات ها تشکیل می شوند.
عوامل موثر در میزان کربناسیون
1- شرایط محیطی
2- تخلخل پوشش بتن
3- مقدار سیمان و تاثیر سیمان های پوزولانی
تبیین بتن بادوام
تبیین بتن بادوام با شناسایی شرایط محیطی آغاز می شود. ابتدا باید مشخص کنیم بتن در معرض چه مکانیسم های تخریب قرار می گیرد؟
سه کلاس قرار گرفتن در شرایط محیطی مربوط به حفاظت از خوردگی آرماتور در ACI 318 تعریف شده است:
1-ملایم (C0)
2-متوسط (C1)
3-شدید (C2)
شایع ترین علت خوردگی فولاد ، نفوذ کلرید است.هرگونه بتن مسلح در معرض رطوبت و کلریدهای خارجی ، چه از طریق آب دریا و چه نمک ، در یک محیط خوردگی شدید در نظر گرفته می شود. این شرایط به حداقل مقاومت طراحی 5000 psi و حداکثر نسبت آب به سیمان 0.4 نیاز دارد. بعلاوه ، استفاده از مواد سیمانی تکمیلی در هر محیطی که بتن در معرض نمک و یخ زدگی و ذوب شدن بسیار شدید باشد ، محدود است.
محدودیت های فعلی عبارتند از:
1- سرباره- حداکثر 50 درصد ،
2- خاکستر بادی - حداکثر 25 درصد
3- بخار سیلیس - حداکثر 10 درصد.
بعلاوه ، مخلوط های حاوی سه یا بیشتر مواد سیمانی یا پوزولانی (سه تایی ، چهار و غیره) در هنگام وجود سرباره بیش از 50 درصد از نظر جرم محدود می شوند یا در صورت عدم وجود سرباره به 35 درصد محدود می شوند .
( Caldarone 2005 ) مشخصات راهنمایی را ارائه می دهد که پذیرش بتن را بر اساس عملکرد امکان پذیر می کند. با توجه به مقاومت در برابر خوردگی ، روش عمل آوری و سن نمونه های آزمایش و با استفاده از ASTM C1202 ،
(RCPT) روش آزمون استاندارد برای نشان دادن توانایی بتن در برابر نفوذ یون کلریدرا نشان می دهد. زیرا همانطور که قبلاً ذکر شد ، نفوذ کلرید مهمترین علت تقویت خوردگی فولاد است. سایر الزامات عملکردی مانند مقاومت در برابر پوسته شدن ، مقاومت و دوام یخ زدگی و ذوب شدن را نیز با آزمایش می توان تعیین کرد.
عوامل داخلی مؤثر بر خرابی های بتن
• نفوذ پذیری بتن
• عوامل مؤثر در نفوذ پذیری بتن
• نسبت آب به سیمان
• تخلخل بتن
• درجه هیدراتاسیون
• خواص سیمان
• اثر دما : با افزایش دما میزان نفوذ پذیری افزایش می یابد.
• واکنش قلیایی سنگدانه ها (برای واکنش قلیایی سنگدانه ها باید اجزای فعال و واکنش زا در سنگدانه باشد و رطوبت و قلیاییت کافی K2O ، Na2O در بتن وجود داشته باشد.)
• فساد مصالح ( وجود بیش از حد املاح در مصالح تشکیل دهنده بتن )
• آب مصرفی
• کیفیت و نوع سنگدانه
عوامل خارجی مؤثر بر خرابی های بتن
تاثیر هوای سرد و یخ زدگی
آزمایشات مقاومت بتن در برابر خوردگی
اولین خط دفاعی در برابر خوردگی آرماتورها جلوگیری از نفوذ آب ، اکسیژن ، دی اکسید کربن و نمک ها از سطح بتن به آرماتور است. با چند آزمایش سعی می شود نفوذ پذیری ، نفوذ ، جذب ، یا سایر اقدامات مستقیم مقاومت به نفوذ مایع را ارزیابی کنید. بیشترین استفاده ASTM C1202 است. این آزمایش معمولاً به عنوان تست نفوذپذیری سریع کلرید (RCPT) شناخته می شود. RCPT اندازه گیری بار الکتریکی است که در طی یک دوره شش ساعته بین دو طرف نمونه بتنی حرکت می کند. این بار مربوط به یون های کلرید است که از طریق سیستم منافذ عبور می کنند. مقادیر پایین بیانگر مقاومت بالاتر در برابر نفوذ کلرید است. اجرای این آزمایش بسیار سریعتر از ASTM C1556 است ( تعیین ضریب انتشار ظاهری فله مخلوط های سیمانی توسط پخش انبوه)
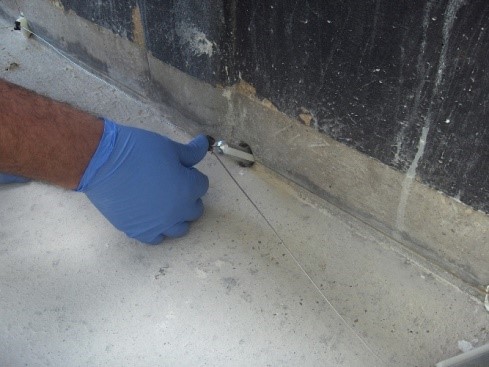
ASTM C1556 روش دقیق تری برای محاسبه نفوذ پذیری بتن است. نتایج آزمون C1556 معمولاً تنوع کمتری را در نتایج آزمون فراهم می کند. نمونه ها پس از 28 روز مرطوب شدن ، تحت نفوذ کلرید یک طرفه قرار می گیرند. عمق نفوذ کلرید با گذشت زمان (با شروع 35 روز خیساندن) با آسیاب کردن لایه های پی در پی از نمونه و سپس اندازه گیری سطح کلرید هر لایه با استفاده از ASTM C1152 ، روش آزمون استاندارد کلرید محلول در اسید در ملات و بتن اندازه گیری می شود. این روش ارتباط مستقیمی با نفوذپذیری بتن دارد و یک روش مفید برای مقدماتی سازی مخلوط های بتن در نظر گرفته می شود. متأسفانه C1556 بسیار وقت گیر است و تکمیل آن به حدود سه ماه زمان نیاز دارد. ASTM C1543 روش آزمون استاندارد برای تعیین نفوذ یون کلرید در بتن توسط استخر ، برای دهه ها توسط بسیاری از ازمایشگاه ها استفاده شده است. دال بتونی به مدت 14 روز ریخته و مرطوب می شود ، سپس تا 28 روز عمل آوری می شود. سطح فوقانی به مدت 90 روز با محلول نمک تخلیه و استخراج می شود. سپس نمونه ها از سطح در معرض گرفته شده و به صورت دیسک های ضخیم تقریباً نیم اینچی برش داده می شوند. هر دیسک خرد شده و مقدار کلرید هر لایه تعیین می شود. متأسفانه ، انجام این آزمون تقریباً به شش ماه زمان نیاز دارد و هیچ روش روشنی برای تفسیر نتایج در روش ارائه نشده است. در AASHTO TP 64 ، پیش بینی نفوذ کلرید در بتن سیمان هیدرولیک با روش مهاجرت سریع ، یک نمونه بتن به طول 2 اینچ و قطر 4 اینچ با استفاده از روش اشباع خلا RCPT انجام می شود. این آزمایش چندین بتن را به همان ترتیب ASTM C1202 درجه بندی می کند ، اما این مزیت را دارد که تحت تأثیر مواد مخلوط شدیدا یونی مانند نیتریت کلسیم قرار نگیرد. همچنین ، نمونه در طول آزمایش افزایش دما را تجربه نمی کند. همچنین نشان داده شده است که این آزمون تا حدودی از تنوع کمتری نسبت به RCPT برخوردار است (Hooton 2001). یک آزمایش سریعتر برای نفوذ پذیری نسبت به RCPT توسط اداره حمل و نقل فلوریدا در سال 2004 ساخته شده است. در این روش از روش ورنر برای آزمایش مقاومت بتن بر روی نمونه های 8 * 4 اینچ استفاده می شود. (ACI 222R 2001) همچنین استفاده از این روش را برای ارزیابی نفوذ پذیری بتن درجا توصیه می کند. نتایج آزمون مقاومت الکتریکی با سیستم درجه بندی نفوذپذیری RCPT ارتباط دارد. مقاومت سطح در عرض چند ثانیه اندازه گیری می شود و بدین ترتیب اندازه نمونه بسیار بزرگتر امکان پذیر می شود. استاندارد فلوریدا به هشت آزمایش در هر سه نمونه احتیاج دارد ، در حالی که RCPT فقط می تواند یک آزمایش واحد در هر نمونه ارائه دهد.
کنترل کيفيت جهت کاهش خوردگی بتن
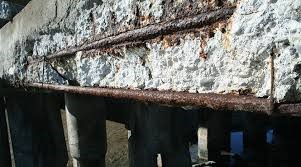
شرايط مصالح از نظر نوع ، کيفيت و آلودگی به عناصر زيان آور در ساخت بتن با دوام بسيار مؤثرند . برای مثال بر اساس آئين نامه بتن ايران ، مواد رد شده از الک نمره 200 که شامل رس و شيل است بايد به 3 و 5 درصد به ترتيب برای بتن های معمولی و تحت سايش محدود گردد. وجود رس و شيل در افزايش جمع شدگی و کاهش مقاومت مؤثرند . همچنين اين مواد در کارآيی بتن اثر گذاشته و سبب افزايش آب مخلوط برای رسيدن به اسلامپ مورد نظر می گردد. در نتيجه نسبت آب به سيمان افزايش يافته و دوام بتن کاهش می يابد. دپوهای سنگدانه ها از نظر آلودگی به عناصر مخرب مانند کلريدها و سولفات ها بايد مورد آزمايش قرار بگيرند و مقدار اين مواد مخرب بايد در حد مجاز و طبق آئين نامه بتن ايران باشد . مقدار رطوبت سنگدانه ها بايد بطور پيوسته مورد آزمايش قرار بگيرد . در اکثر مواقع ، تغييرات در کارآيی و مقاومت در پيمانه های مختلف به دليل منظور نکردن تغييرات رطوبت سنگدانه ها رخ می دهد . وضعيت آرماتور نيز نقش عمده ای در دوام سازه دارد . اگر بر روی سطح ميلگردها قشر بسيار نازک زنگ به صورت يکنواخت مشاهده شود ، استفاده از آنها در سازه بدون اشکال است ، زيرا اين زنگ سبب افزايش پيوستگی بتن به آرماتور می شود ، از طرف ديگر ، خمير سيمان به دليل قليايی بودن قادر است که اين لايه را به قشر محافظ تبديل کند . اما در صورتی که قشر زنگ بر روی ميلگردها با ضخامت زياد باشد ، نه تنها از قطر ميلگردها کاسته می شود ، بلکه پيوستگی کاهش می يابد . از طرف ديگر بتن قادر نيست که قشر ضخيم زنگ را به لايه محافظ تبديل کند . بخصوص اگر خوردگی از نوع حفره ای باشد ، تحمل تنش در محل حفره ها کاهش يافته و پايداری سازه بطور جدی در معرض خطر خواهد بود . انتخاب نوع سيمان نيز در دوام سازه اثر دارد . سيمان مصرفی بايد قادر باشد تا در شرايط مختلف سازگار باشد و مقاومت و دوام مورد نظر را تأمين کند . اگر شرايط محيطی معمولی باشد ، می توان با انتخاب نوع سيمان به خواص مورد نظر دست يافت ، اما در شرايط سخت ، نياز به اهرم های ديگر مانند کاهش نسبت آب به سيمان و استفاده از مواد افزومدنی معدنی ( پوزولان ها ) و شيميايی مناسب است . ترکيب C3A در سيمان نقش مهمی در تهاجم سولفات ها ، ترک خوردگی ناشی از جمع شدگی خميری و خوردگی آرماتور دارد . اما اين ترکيب به تنهايی نمی تواند با تمام عوامل تهديد کننده دوام مقابله کند ، بخصوص آنکه شرايط محيطی بسيار سخت باشد ، به همين دليل استفاده از يک سيستم دفاعی مانند پوزولان ها غير قابل اجتناب است . اما برای بهبود خواص و دوام بتن نبايد بدون در نظر گرفتن نوع ، کيفيت و مقدار مناسب جايگزينی از پوزولان استفاده کرد . اگر ترکيبات و خواص پوزولان مورد نظر مورد بررسی قرار نگيرد ، نتيجه حاصل ممکن است عکس نتيجه مورد انتظار باشد.
ملاحظات اجرايی بتن در هوای گرم و مرطوب
انتقال بتن آماده توسط تراک ميکسر در هوای گرم مشکلات خاصی را به مراه دارد . بر اساس ASTM C 94 ، در دمای معمولی C 020 ، حداکثر تعداد چرخش جام تراک ميکسر با سرعت مخلوط کن بايد به 100 دور محدود شود و چنانچه تعداد دور بيشتر لازم باشد ، بايد سرعت را کاهش داد. سرعت مخلوط کردن و بهم زدن متفاوت است . سرعت بهم زن معمولا 2 تا 6 دور در دقيقه و سرعت مخلوط کن بين 6 تا 18 دور در دقيقه است. طبق ASTM C 94 بايد قبل از 5/1 ساعت يا قبل از 300 دور چرخش جام ، بتن را ریخت. در ASTM 305 توصيه شده ، که در هوای گرم تعداد چرخش جام و مدت چرخش محدود گردد ، در غير اين صورت افت اسلامپ افزايش قابل توجهی می يابد . در صورت افت شديد اسلامپ ، افزودن آب به مخلوط اجتناب ناپذير می گردد و در نتيجه افزايش نسبت آب به سيمان ، دوام بتن کاهش می يابد.
يکی از مهمترين عوامل آسيب رسان بتن در هوای گرم ، ترک خوردگی در اثر جمع شدگی خميری است . سطوح بتن تازه در معرض تبخير و افت آب مخلوط قرار می گيرند . ميزان تبخير تابع شرايط محيطی مانند دما ، سرعت باد و رطوبت نسبی است . معمولا کاهش آب ناشی از تبخير با آب حاصل از آب انداختن جايگزين می گردد . اگر سرعت تبخير بيشتر از سرعت آب انداختن باشد ، در لايه سطحی بتن کاهش حجم ايجاد می شود . لايه زيرين بتن در مقابل کرنش حاصل از کاهش حجم ، مقاومت می کند . قيد ايجاد شده از لايه زيرين سبب ايجاد تنش های کششی در لايه سطحی شده و از آنجایی که مقاومت کششی بتن در سنين اوليه کم است ، بتن ترک می خورد. بر اساس ASTM 305 چنانچه سرعت تبخير بيشتر از 1کيلوگرم بر متر مربع بر ساعت باشد ، احتمال ترک خوردگی افزايش می يابد .
برای کاهش جمع شدگی خميری موارد زير توصيه می شود :
• مرطوب کردن سنگدانه
• نصب موقت باد شکن و سايه بان
• کاهش دمای بتن تازه با سرد کردن سنگدانه ها و آب مخلوط
• محافظت از سطح بتن با پوشش های موقت مانند ورق پلی اتيلن پس از جاگذاری بتن و عمليات پرداخت
• تراکم مجدد بتن
در هنگام استفاده از دوده سيليسی در بتن بايد توجه داشت که چسبندگی اين نوع بتن زياد و در نتيجه عارضه آب انداختن در آن کمتر از بتن معمولی است . بنابراين احتمال ترک خوردگی ناشی از جمع شدگی خميری بيشتر است ، بويژه اگر سرعت تبخير آب زياد باشد. در هنگام استفاده از دوده سيليسی بايد عمل آوری بلافاصله پس از بتن ريزی آغاز گردد. اجرای صحيح مراحل مختلف پرداخت ، در افزايش مقاومت سايشی و دوام لايه سطحی بتن نقش قابل توجهی دارد . از نظر دوام ، ماله کشی با ماله بايد قبل از مشاهده آب انداختن به اتمام برسد . بطور کلی ، اگر هر مرحله از پرداخت در زمان آب انداختن اجرا شود ، سبب پوسته شدن لايه سطحی بتن شده و مقاومت سايشی و دوام بتن کاهش می يابد . بنابراين ادامه عمليات پرداخت بايد پس از تبخير آب از سطح بتن صورت پذيرد . برای آنکه بتن مقاومت و دوام مورد نظر را کسب کند ، عمل آوری بايد به نحو مطلوب صورت پذيرد . روش های مختلفی برای عمل آوری بتن مورد استفاده قرار می گيرند که می توان آنها را به دو گروه تقسيم کرد . در روش عمل آوری با آب ، رطوبت اضافه به بتن اعمال و از افت رطوبت نيز جلوگيری می شود. برای اعمال آب بر سطح بتن از ايجاد حوضچه يا افشاندن و يا از پوشش های اشباع مانند چتايی خيس استفاده می شود . در روش عمل آوری عايقی ، از افت بتن جلوگيری می شود . از ورق های پلاستيک و مواد شيميايی غشايی می توان برای جلوگيری از کاهش رطوبت بتن استفاده کرد. قالب ها نيز به صورت عايق عمل می کنند و مانع تبخير آب بتن می شوند . بر اساس توصيه ASTM 305 ، هوای گرم و خشک ، قالب های چوبی نمی توانند از تبخير آب جلوگيری کنند و در صورت استفاده از اين نوع قالب ها ، بايد آنها را با پوشش مناسب و مرطوب محافظت کرد. به طور کلی در مواردی که بتن دارای نسبت کم آب به سيمان است و بخصوص از ميکروسيليس استفاده می شود ، روش عمل آوری با آب به عمل آوری عايقی ترجيح داده می شود زيرا در اين نوع بتن ها امکان خود جمع شدگی وجود دارد و در نتيجه امکان ترک خوردگی افزايش می يابد. اين عارضه بخصوص در هوای گرم بيشتر مشاهده می شود.
به طور کلی در شرايط محيطی و اقليمی گرم و مهاجم ( از نظر مجود عناصر مخرب ) ، برای افزايش دوام سازه های بتن آرمه ، توصيه می شود موارد زير در هنگام ساخت رعايت گردد :
• شستشوی مصالح سنگی برای کاهش مقدار رس و شيل
• وجود عناصر مخرب مانند کلريدها و سولفات ها در مصالح در حد مجاز طبق آئين نامه ها
• انتخاب نوع مناسب سيمان و مواد افزودنی معدنی و شيميايی
• استفاده از ميلگردهای بدون زنگ يا با زنگ بسيار کم
• سرد کردن مصالح مصرفی بتن بخصوص آب مخلوط
• کاهش زمان انتقال بتن برای جلوگيری از افت اسلامپ
• محافظت و عمل آوری مطلوب
پوشش های ضدخوردگی بتن
در کنار روش های متداول برای جلوگیری از نفوذ پدیری و خوردگی بتن و آب بند نمودن آن استفاده از سیمان های پوزولان طبیعی و مصنوعی ، میکرو سیلیس ، حفاظت کاتدی ، پوشش آرماتور ها با رزین اپوکسی ، استفاده از ورق های محافظ آلیاژی ، آرماتورهای آلیاژی و کامپوزیت و ورقه های ، کاربرد ژئو سنتتیک ها استفاده از پوشش بتنی محافظ و بتن پلیمری ، یکی از روش های مقرون به صرفه و مؤثر استفاده از پوشش های صنعتی است. مشکل اول مواد خورنده ای است که در دراز مدت به داخل بتون نفوذ کرده است و چسبندگی بتن جدید را با سطوح بتونی قبلی مختل میکند . مشکل دوم این است که بطور کلی بتن جدید به بتن قدیمی خوب نمیچسبد. خنثی سازی مواد خورندهای که به داخل بتون نفوذ کرده است بسیار مشکل بوده و همچنین پر هزینه میباشد. در صورتی که بتوان تا حدودی در این مورد هم موفق بود ، باز نمی توان از واکنش بین مواد شیمیایی که هنوز در داخل بتن مانده اند با پوشش های حفاظتی که بعدا بر روی بتن اجرا شده اند جلوگیری کرد چرا که این واکنش ، باندینگ بین پوششها و سطوح بتونی را سست می کند و در نهایت پوشش از روی سطح کنده می شود. بنابراین باید سطوح را از قبل آماده نمود تا اطمینان از چسبندگی مناسب رنگ به سطح و افزایش چسبندگی به علت افزایش سطح و اقزایش گروه های فعال سطح در واحد سانتیمتر مربع اتفاق افتد. همچنین اطمینان از اینکه واکنش بین رنگ و سطح در اثر حضور یون های فعال نظیر کلریدها وسولفات ها شکسته و تخریب نشود که با توجه به خورنده بودن محیط توجه بیشتری می طلبد.
روش های برای آماده سازی سطح روش های مختلفی وجود دارد از ان جمله روش های مکانیکی نظیر فشار بخار مایع ( بخار آب تحت فشار) و ساینده های تحت فشار(سند بلاست) ، هوای متراکم ، فشار مستقیم و ثقل ، سایش با ورقه های سمباده کاغذی و فلزی و ابزارهای دستی چون برس سیمی ، کاردک کم عرض قلم چکش ، چکش لبه تیز و ابزارهای الکتریکی (ضربه ای- چرخشی) پاشیدن آب تحت فشار (واترجت) و استفاده از سود برای واکنش با سولفات و کلرید سطحی و تشکیل نمک و شستشو با آب می باشد.
روش دیگر پاشیدن ساینده ها به دو صورت جریان هوای متراکم و نیروی چرح دوار یا نیروی گریز از مرکز می باشد. عوامل تعیین کننده در میزان فشار پاشیدن ، انرژی ذرات ساینده پرتاب شده، زاویه برخورد ساینده با سطح کار ، سختی سطح کار ، سختی ساینده می باشد.
درصنعت ۳ سیستم ابزار مختلف وجود دارد.
• سیستم معمولی پاشیدن ساینده خشک
• سیستم پاشیدن در خلاً
• سیستم پاشیدن ساینده مرطوب
برای انتخاب ساینده مناسب موارد ی را باید در نظر گرفت ، اندازه ، شکل ، ترکیب شیمیایی ، PH ، درصد رطوبات موجود ، درصد روغن موجود ، رنگ ، ثبات وزن در اثر حرارت ، وزن مخصوص ، قابلیت تهیه ، قیمت و سختی ساینده ها به ۲ دسته
1- معدنی (طبیعی)
2- سربار فلزی تقسیم می کنیم.
تقسیم بندی ساینده ها براساس درصد بلور سیکا انجام می گیرد که از طیف سنجی مادون قرمز بدست می آید . روش های شیمیایی شامل حلال شویی ، اسید شویی ، قلیا شویی ( مثل هیدروکسید سدیم ) ، شستشو با محلول های الکترولیتی ، استفاده از رنگ برها و ترکیبات تشکیل دهنده کمپلکس آلی فلزات روش های حلال شویی : مالیدن حلال از طریق پارچه یا برس – اسپری – غوطه وری سطح کار قابل حمل در حوضچه یا تانک حلال – روغن زدایی با بخار حلال است. همچنین اسیدشویی از طریق اسیدسولفوریک ، کلریدریک ، نیتریک ، فلوئوریدریک و فسفریک در 3 مرحله انجام می شود:
1- آماده سازی قبل از اسید شویی
2- شستشو با اسید
3- شستشوی سطح تمیز شده پس از اسید شویی.
رنگ برها هم نوع دیگری از ساینده ها هستند که رنگبرها به ۲ دسته
1- آلی (مثل متیل کلراید)
2- معدنی تقسیم می شوند.
در فرمولاسیون رنگبرها
1- مواد فعال کننده سطحی جهت کاهش سطحی مایع
2- الکل ها جهت نفوذ در لایه رنگ و تورم و جداسازی آن از سطح
3- اسیدگلونات ویا نمک های آن جهت جدا شدن رنگ از سطح ( آب ، الکل هاو گلیکول اتر) وجود دارد.
تمیزکاری انرژیک
1- با استفاده از انرژی حرارتی شعله
2- استفاده از امواج ماورا صوت
3- استفاده از لامپ
4- استفاده ازاشعه لیزر
5- استفاده ازپلاسمای گاز گرم
6- استفاده از جت اسفنجی انجام می شود.
برای استفاده از آستری پس از تمیز کاری سطح می توان از واش پرایمر ، فسفاته کردن شامل فسفات روی و فسفات آهن و کروماته کردن استفاده کرد. خواص آستری های کارگاهی ایجاد چسبنگی خوب در سطح فلز ، مقاومت لازم و کافی در مقابل خوردگی فلز ، زمان خشک شدن کوتاه ، مقاومت در مقابل ضربه و ترک خوردگی ، مقاومت در برابر سایش ، قابلیت پرکنندگی حفره ها و چسبندگی به پوشش بعدی است. بخش های مختلف تشکیل دهنده یک پوشش ۱-رزین ها ۲- رنگدانه و پرکننده است که شامل حفاظتی نظیر پودر روی و فسفات و یا با اثر خاص می باشد . مواد افزودنی واصلاح کننده رقیق کننده ها ، نرم کننده ها ، شتاب دهنده ها ، بهبود دهنده های سطحی شامل رقیق کننده ، نرم کننده ، شتاب دهنده و بهبود دهنده سطحی می باشند.
بتونه ماستیک وحلال مایعات شیمیایی فراری هستند که برای رقیق کردن رزین به آن افزوده می شود و در انتخاب حلال مناسب بایستی به
1- قدرت حلالیت
2- سرعت تبخیر
3- نقطه جوش
4- نقطه اشتعال و قابلیت شعله وری
5- سمیت آن توجه داشت.
طبقه بندی حلال ها بصورت
1- ترپن ها
2- هیدروکربن ها (نفتیک مثل وایت اسپریت ، آلیفاتیک و آروماتیک مثل تولوئن و ترکیات آن نظیر تولوئن دی ایزو سیانات TDI ، تری نیترو تولوئن TNT ، زایلن و منومر استایرن (وینیل بنزن) )
3- حلال های اکسیژندار الکل ها هیدروکسیل مثل متانول ، اتانول ، بوتانول ، گلیکول ها و گلیسرول ها و . . . ، اترها ، کتون ها مثل استون ، استرها
4- نیتروپارافین ها
5- حلال های کلر دار
خواص آنها عبارت است از
1- وزن مخصوص بالا
2- قابلیت اشتعال کم
3- بوی خاص
4- خواص بیهوش کننده و سمیت زیاد
5- قدرت حلالیت زیاد
از هاردنر یا سخت کننده برای اصلاح برخی از خواص رزین از هاردنر استفاده می شود به عنوان مثل برای رزین اپوکسی از پلی آمین ، پلی آمید ، استر ، وینیل و کولتار از مشتقات قطران
انواع رزین بصورت زیر می باشند :
طبیعی به صورت خام در طبیعت یافت می شود صمغ وشیره درختان ، رزین های فسیلی می باشد یکی از آنها رزین کولتار است که از قطران بدست می آید و برای اصلاح و بهبود مقاومت و نفوذ ناپذیری رزین اپوکسی و پلی اورتان بکار میرود. مصنوعی سنتزی از نوع
آلکیدی از پلی ال ، پلی اسید و اسید چرب (روغن) تشکیل شده و پلی ال الکل با بیش از دو هیدروکسیل(مثل گلیسرین) و پلی اسید ، اسید آلی با دو یا چند عامل کربوکسیل یا انیدرید ( مثل انیدرید فتالیک) تشکیل شده است .
روغن ها به ۳ دسته
1- خشک شونده (مثل روغن برزک و ماهی)
2- نیمه خشک شونده (مثل سویا و تال)
3- غیر خشک شونده (مثل نارگیل ، کرچک و پنبه دانه)تقسیم بندی می شوند.
کلرو کائوچو : کائوچو در طبیعت نئوپرن یا ایزوپرن با فرمول کلی پلیمری با زنجیره فنر مانند که خاصیت ارتجاعی دارد. اپوکسی نوعی رزین ترموست ( گرما سخت) می باشد. و ازمشتقات پلی آمین می باشد .
بیس فنول A : از واکنش فنول و استون بدست می آید.
بیس فنول F : از واکنش تراکمی فنول یا کروزل با فرمالدئید بدست می آید.
اپوکسی نووالاک : با افزایش زنجیره بیس فنول F تشکیل می شود.
اپوکسی آلیفاتیک : از پلی ال های خطی ( آلیفاتیک) به واسطه با ویسکوزیته پایین به عنوان رقیق کننده فعال برای سیستم اپوکسی بدون حلال کاربرد دارد .
اپوکسی سیکلو آلیفاتیک و هتروسیکلیک ، فنوکسی : در زنجیره خود بجای ۲ گروه اپوکسی انتهایی فنول دارد. واکنش با عوامل شیمیایی و ایجاد تغییرات در رزین اپوکسی. واکنش با انیدرید پلی کربوکسیلیک اسید ، اسید چرب وپلی فنول ، ایجاد شبکه ۳ بعدی و عرضی (Cross Link) با آمین ها ازطریق اضافه کردن هاردنر (سخت کننده) پلی آمین به رزین ،کتیمین (واکنش یک کتون با پلی آمین) ، رزول و آمینوپلاست ، پلی ایزو سیانات و پلی سیلوکسان و کاتالیزور آنیونی یا کاتیونی ونسبت اختلاط رزین و هاردنر در اپوکسی ۲ جزئی براساس عدد پاپوکسی وآمین اکی والان تعیین می شود که برای داشتن پیوند مناسب رعایت نسبت اختلاط براساس دستورالعمل کارخانه های سازنده حاپز اهمیت است نسبت اختلاط در Pot life گیرش اولیه پس از ۵ دقیقه واکنش گرمازا (شبیه به واکنش سیمان با آب در بتن) حالت ژل و فیلم سخت ایجاد می گردد ، تأثیر دارد.
ترمیم بتن در معرض خوردگی
چنانچه سازه های بتنی تحت شرایط محیطی شدید قرار گرفته و دچار خوردگی شوند ، حفاظت بسیار مشکل و پر هزینه تر از زمانی است که در مراحل طراحی اولیه پوشش مناسب در نظر گرفته شود. سازه های بتنی جدید نیز که هنوز در معرض مواد شیمیایی خورنده قرار نگرفته اند می بایست دارای شرایطی باشند که بتوان بر روی آنها پوشش های ضد خوردگی را اجرا نمود .پوشش ها و لاینینگ های ضد خوردگی می بایست به صورت محکم و مطمئن به سطوح بتنی زیر کار بچسبند که در این خصوص سازه بتنی باید طوری ساخته و اجرا گردد که دارای ماکزیمم قدرت نگهداری پوشش و نیز از مقاومت کششی خوبی برخوردار باشد. به طور کلی پوشش ها و لاینینگ های حفاظتی پشتیبان و نگهدارنده خود نمیباشند (به جز لاینینگ داخل پیت ها و مخازن که در آنجا پوشش از یک خود پایداری و ایستایی مناسب برخوردار می باشد) و معمولاً در مقابل تنش های خمشی ضعیف عمل می کنند. بنابراین سازه بتنی مسلح باید بتواند تا حد امکان از تغییر شکل های ناشی از بارهای خمشی و ارتعاشی جلوگیری کند همچنین می بایست از ایجاد ترک در بتون که ناشی از نشست و یا انقباض بتون می باشد و نیز بارهای تنشی جلوگیری گردد.
با توجه به اینکه پوشش ها و مواد حفاظتی دارای مشخصات فیزیکی بسیار متفاوت با بتون می باشند لذا بارهای وارد بر آن می بایست در نظر گرفته شده و محاسبه گردد. به خصوص زمانی که سازه بتنی تحت تاثیر دماهای بالا قرار می گیرد. ساختمان باید مطابق با قوانین جاری برای تحمل کلیه بارهای قابل انتظار شامل تنشهای حرارتی به درستی محاسبه گردد. در ضمن در صورتی که قرار باشد یک لایه حایل یا بازدارنده (membrane) بر روی بتون اجرا گردد، باید از ایجاد ترک در آن که معمولا در کارهای ساختمانی معمولی مجاز میباشد تا حد امکان اجتناب گردد. جزئیات نقشه آرماتور بندی باید به دقت بر طبق محاسبات (مقاومت در مقابل گشتاورها و نیروهای برشی ، عدم وجود تانکر فولادی حمل بار در منطقه تنش کششی و غیره) اجرا گردند. قالب بندی ، ریختن و فشرده سازی بتون و خم کردن، قرار دادن و اتصال آرماتورها باید در محل ساختمان مطابق با نقشه مهندس ساختمان اجرا گردد.در صورتی که موارد ذکر شده در سازههای در معرض مواد شیمیایی خورنده رعایت نگردد، عواقب بسیار خطرناکی به وجود خواهد آمد.پوشش ناکافی بتن بر روی آرماتوربندی اجرا شده و نیز بر هم خوردن مخلوط بتن به هنگام ریختن باعث تجمع شن و ماسه در مناطقی می گردد. تجمع ماسه نه تنها در موارد متعددی باعث تضعیف ظرفیت تحمل بار بتن می گردد بلکه نفوذ مواد خورنده به داخل بتون و در نتیجه خوردگی آرماتور بندی داخل بتن را تسهیل می کند. همچنین این مشکل اجرای صحیح لایه membrane و پوشش های رزینی سینتتیک را نیز مختل می کند. نتیجه دیگر تغییر مخلوط بتن در هنگام بتون ریزی این است که سطوح رویه بتن عموما از دوغاب و دوغاب سیمانی که دارای ذرات بسیار نرم تشکیل می گردد. این سطوح صاف دارای مقاومت فشاری مناسبی نبوده و همچنین هیچ مقاومت کششی ندارند. این سطوح ، سطح زیر کار مناسبی به دلیل عدم وجود چسبندگی برای اجرای پوشش های رزینی به عنوان مثال لایه های ماله کشی نمی باشند.
در واقع حتی برای رنگ های قیری سرد معمولی و یا برای شیت هایی که چسبانده می شوند نیز از استحکام و چسبندگی کافی برخوردار نیستند.همچنین سطوح بتنی صاف که در نتیجه استفاده از مواد کمکی برای جدا شدن قالب بندی و استفاده از قالب بندی فولادی حاصل می گردند علی رغم جذابیت و زیبایی که دارند؛ سطوح مناسبی جهت اجرای پوشش های رزینی نمی باشند. ضمن اینکه روغنی که جهت قالب بندی استفاده می گردد از چسبندگی بین بتن و پوشش های جلوگیری می کند. تجربه نشان داده است که بهترین سطوح بتونی جهت اجرای پوشش ها حفاظتی، سطوحی است که به صورت تخته ماله ای (ماله چوبی) اجرا شده است چرا که از لحاظ زبری مناسب بوده و حداکثر باندینگ مکانیکی را با پوشش برقرار میکنند. در صورتی که سطوح بتنی با روش قالببندی فلزی اجرا شده باشند و میبایست با روشهایی مانند سند بلاست به زبری مورد نیاز رسید.با توجه به استاندارد ACI318 که استاندارد و روش های آماده سازی و اجرای سازه های بتنی را بیان میکند. یک سازه بتنی میبایست دارای مقدار خاصی از سیمان و نیز دارای توزیع مشخص دانه بندی باشد. همچنین ضروری است که بتون تازه چنان حمل گردد و یا به داخل قالب ریخته شود و در نهایت متراکم گردد که مخلوط آن بر هم نخورد. تنها در این صورت میتوان مطمئن بود که به مقاومت فشاری مورد نیاز و مقاومت کششی کافی (تقریبا برابر یک دهم مقاومت فشاری) دست خواهیم یافت. اگر چه مقاومت کششی بتون معمولاً در طراحی ساختمان های بتون مسلح در نظر گرفته نمیشوند.
در صورتی که این مقاومت عامل تعیین کننده ای در پایداری پوشش ها و نیز هزینه های آن خواهد داشت.همچنین باید توجه داشت که در زمان حمل، بتون ریزی و متراکم سازی بتن ، نسبت آب به سیمان بتن با استفاده از افزودنی های مناسب به اندازه کافی پایین نگه داشته شود. این کار از جدا شدن سیمان و نیز دانه بندی های شن و ماسه جلوگیری می کند. در زمان اجرای سطح کف بتونی ، کف کانال ها و سامپ ها می بایست شیب بندی مناسب براساس نیاز ایجاد گردد. چرا که شیب بندی بعد از اتمام بتن ریزی اصلی ، بدلیل استفاده از پلاسترهای سیمانی که دارای ضخامت کمی بوده و نیز از چسبندگی مناسب به سطوح بتنی قدیمی برخوردار نیستند ، توصیه نمی گردد. ضمن اینکه پلاسترهای سیمانی دارای مقاومت های لازم فشاری و کششی نمی باشند. تجربه نشان داده است که در زمان بتون ریزی هیچیک از مجریان و ناظرین بتون ریزی به شیب بندی توجه ای ندارند و این در حالی است که پس از انجام کاشی کاری ضد اسید و یا اجرای پوششهای رزینی حساسیت به شیب مورد نیاز برای همان مجری و یا ناظر بیشتر می شود. اجرای شیب مناسب و مورد نیاز در زمان بتون ریزی بسیار ارزان تر و آسان تر از زمانی است که بخواهیم با مواد پوششی شیب بندی کنیم.
بررسی تعداد زیادی از واحدهایی که محوطههای آنها در معرض ریزش مواد خورنده بوده اند نشان داده است که سطوحی که دارای شیب مناسب بوده اند ولیکن مواد پوششی مورد استفاده بر روی آنها نامناسب بوده است ، بسیار بهتر از سطوحی که در آنها از مواد حفاظتی درست و گران استفاده شده ولیکن شیب بندی رعایت نشده است ، عمل کرده اند. سازه های بتن مسلح بخصوص در کف ها که بر روی آنها از پوشش های ضد خوردگی استفاده شده است. می بایست طوری طراحی گردند که در معرض کمترین تنش ها قرار گیرند. در غیر این صورت تحت یک بار استاتیک به راحتی تغییر شکل می دهند که این تغییر شکل منجر به ترک های کششی اجتناب ناپذیر در محل گشاورهای منفی شده و در نهایت به پوشش حفاظتی منتقل میگردد. به علاوه به علت فرکانس ارتعاشی ذاتی نسبتاً پایین این سازهها، به هنگام قرار گرفتن در معرض بارهای دینامیکی (موتورها ، پمپ ها ، مخلوط کن ها ، کمپرسورها و موارد مشابه) مرتعش می شوند که در چنین حالتی ممکن است سازه بتنی اصلی دارای بار اضافه شده و در نهایت پوشش حفاظتی خسارت ببیند.
شکل و طراحی مخازن بتنی نیز می بایست طوری باشد که بتوان حداکثر ایستایی را برای پوششهای اجرا شده بوجود آورد به عنوان مثال در یک مخزن با دیواره استوانه ای و خمیده میتوان با استفاده از کاشیهای با ضخامت کم به همان مقاومت و ایستایی رسید که با مخزن عمودی و آجرهای با ضخامت بالا میتوان رسید. کاشی های با ضخامت کم بر روی دیواره عمودی به دلیل اینکه نمیتوانند پشتیبانی خود باشند، پایداری ندارند و بر اثر حداقل تنشی از روی سطوح کنده می شوند. کلیه لبه ها ، گوشه ها و کنج های داخلی مخازن بتنی باید گرد شوند زیرا لبهها و گوشه های تیز نقاط خطرناکی برای اجرای لایه ها و پوشش های حفاظتی می باشند. همچنین بهتر است به جای ساخت مخازن بسیار بزرگ که می بایست به دلایل فنی دارای یک یا چند درز انبساط باشد، از چند مخزن کوچک که دو به دو دارای دیوارهای مشترک هستند استفاده گردد. این بدین خاطر است که اجرای درزهای انبساط در مخازن بتنی مسلح محتوی مواد خورنده غالبا با مشکلات بسیار بزرگی همراه است که گاهی نیز غیر قابل حل بوده و ضمن اینکه در صورت وجود راه حل هزینه های آن بسیار بالا است. از مسائل مهم دیگری که در زمان اجرای یک سازه بتنی می بایست در نظر گرفت وجود رطوبت داخل بتون بوده که به هنگام اجرای پوشش ها و یا لایه های حفاظتی مشکلات عدیده ای را بوجود می آورد که چسبندگی پوشش ها به بتن را مختل می کند. این مشکلات خسارات جبران ناپذیری را پس از اعمال پوشش بوجود می آورند.